Medical Supply Distribution Company
Validation Services: Warehouse Environmental Mapping
About Client
Our client is a leading medical supply distributor with facilities located throughout the U.S., serving healthcare providers and hospitals nationwide.
Business Challenge
The NEXA Validation team was contracted to design and execute Winter and Summer Environmental mapping studies for our client’s twenty-nine (29) distribution centers located across twenty-seven (27) states throughout the U.S. The project is being executed in five (5) phases, with Phase 1 launched in June 2022, with an expected completion of March 2023.
The seasonal mapping study is critical for our client to assess storage risk to temperature sensitive products and materials, and to identify and remediate any improper storage conditions. Further it will support audit-readiness for USP and FDA regulatory compliance. Serving as the single source provider, the NEXA team can ensure standardization and develop governing policy for validation methodology across the network of distribution centers.
Project Challenges
Projects of this size and scope presented several challenges that NEXA’s Validation team was uniquely equipped to address.
These include the following:
- Project Management: Coordination of service activities across (29) sites.
- Schedule: Completion of all sites during the 12-week seasonal periods.
- Equipment: Dedicated equipment and logistics expertise to execute four to six (4-6) warehouses concurrently during each phase of the project.
- Staff: Six (6) Validation Engineers were assigned that specialize in environmental mapping studies to execute the winter/summer mapping profiles.
Scope of Work
In working closely with the client, the Validation team leveraged the expertise of NEXA’s Quality team to address a client request for an independent audit of the environmental monitoring and response program. Additionally, the team partnered with the client on the development of the validation method and protocols to meet the client’s risk assessment and budget allocation.
Key deliverables include:
- Development of (5) master protocol templates
- 7-day summer profile for (29) sites
- 7-day winter profile for (29) sites
- 72-hour cold chain mapping for (53) walk-in refrigerators/freezers
- Weekly project status meeting
- Qualification Summary Reports
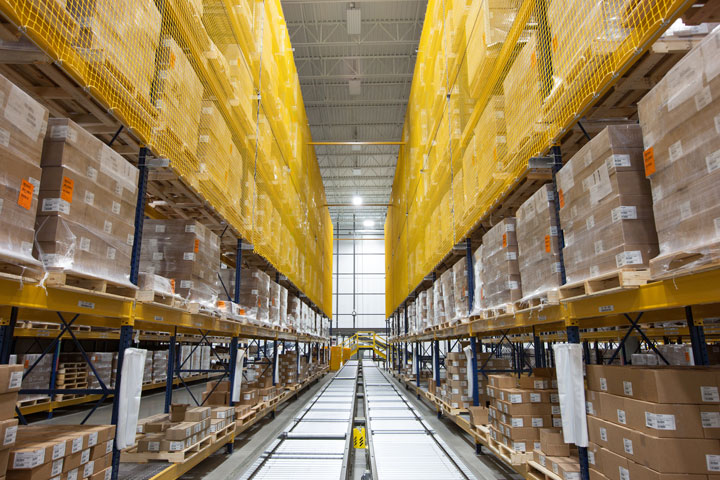
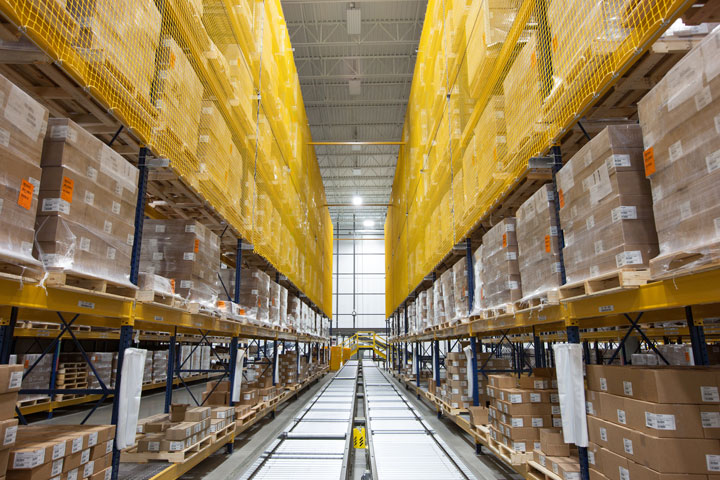
As a result of the NEXA team executing a successful project, the client has requested continued support and partnership to address environmental mapping for their new locations which will be constructed in 2023, as well as planned revalidation efforts. This will assure global quality compliance for the safe storage of their regulated products and materials.
Key Results
Quality Improvements
- Standardized validation methods and reports across all sites
- Single provider enabled consistent deviation management across the enterprise
Migration to Paperless Validation
- Protocol review and approval via online tool
- Valgenesis – 21 CFR Part 11 Validated system
- Approved Qualification Packages delivered as a single PDF
Project Management
- Project oversight by Validation Director
- Single provider enabled simplified and consistent communication plan
- Online Project Management platform for scheduling, status updates, and tracking through project completion