Several changes are being implemented to Transcat's service levels effective March 2021. These changes are a result of the changes to ISO 17025:2017, ILAC P14, and ANSI Z540.3-2006 and NIST's Policy on Traceability. We will try to answer some these questions. Some of these topics will be expanded on in other white papers and FAQ's which can be found above.
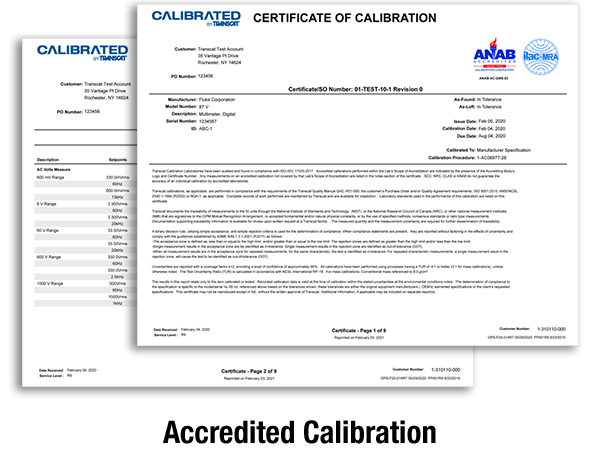
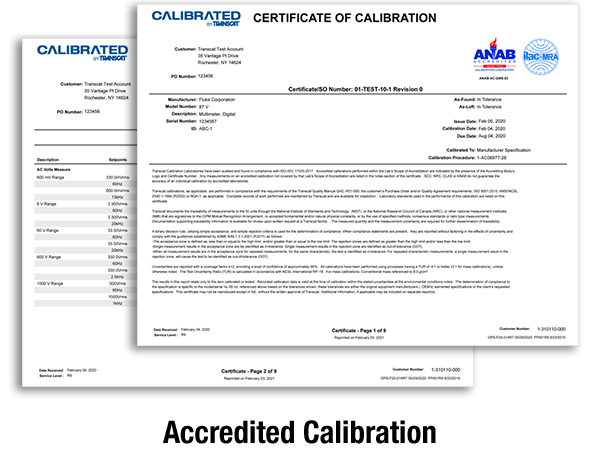
Transcat has previously provided three accredited levels of service. All three levels of our service that we have been providing have been accredited calibrations per the ISO 17025 standard that we have been audited to by our accrediting body (ANAB). Per ILAC (International Laboratory Accreditation Committee) which is the international organization for accreditation bodies, all accredited calibrations must now include measurement uncertainties to be considered an accredited calibration. This change was released in September 2020 and must be implemented by March 31, 2021.
In addition, ILAC P14, ISO 17025:2017, and NIST’s Policy on Traceability all require that calibrations that do not include reported measurement uncertainties prevent the respective instrument from propagating traceability. These changes along with the requirements of Z540.3-2006, we have updated our service levels to provide flexibility to meet our customer’s various quality requirements. The changes to our service levels are detailed here.
Q: I have been receiving a calibration without data (or with data) from you. How does this change affect me?
A: The main differences in these two levels is that you will no longer see an accreditation logo on your certificate and there will no longer be a statement of traceability to SI units on the certificate. Otherwise your calibration will be the same as you have previously been receiving from Transcat. All our calibrations will follow the same processes by the same personnel using the same standards.
Q: If the calibration is the same, why will the certificate not have the accreditation logo on it?
A: As mentioned previously, the international standards, accrediting bodies, as well as NIST have maintained that to have traceability, measurement uncertainties must be provided and without those a calibration cannot be considered accredited.
Q: What if I need to have an accredited calibration?
A: We will still be able to provide you an accredited calibration. You will just need to specify that requirement at the time you place your order.
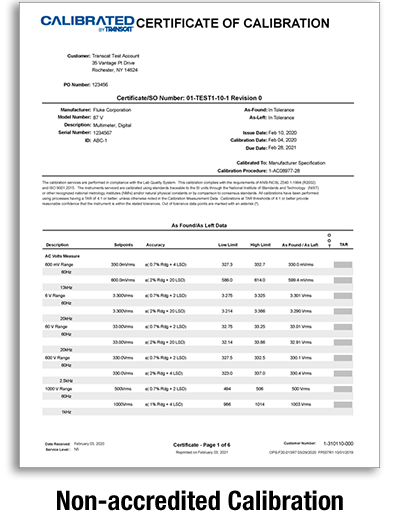
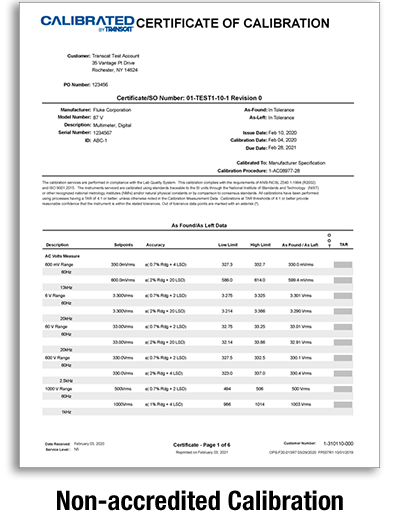
Q: Why are measurement uncertainties important?
A: Because there are no perfect measurements and no perfect instruments. There is always something unknown about every measurement. If you a performing any type of calibration on any device that will, in turn, be used to perform other process measurements, you will be passing along any potential error. This can be thought of as the domino effect: any uncorrected errors and all uncertainties in the calibration measurement process will be passed down to all the measurements made by the calibrated device.
Q: Does every calibration company have to follow these standards?
A: Yes, if they are accredited to the ISO/IEC 17025 standard and the measurement parameter is on their scope of accreditation. If you request an accredited calibration and the accrediting body logo is on the certificate, they must provide the measurement uncertainties. If a company is providing a calibration with an accreditation logo and it does not contain measurement uncertainties then it is in violation of their accreditation.
Q: What if I am not sure about what level of service I need?
A: You can feel free to contact us with any questions and one of our calibration specialists will be happy to discuss your requirements and provide any assistance that we can.
For more information about our accreditation or your calibration requirements, contact one of our calibration professionals at 800-828-1470 or contact us.
Several changes are being implemented to Transcat's service levels. These changes have been necessitated due to the changes to ISO 17025:2017, ILAC P14, and ANSI Z540.3-2006 and NIST's Policy on Traceability. We will try to answer some these questions in this FAQ. Some of these topics will be expanded in other white papers and FAQ's which will be linked below.
Q: What has changed?
A: An accredited lab is one that demonstrates its ongoing competence in the field of calibration and/or testing that meets the requirements of ISO/IEC 17025 General Requirements for the Competence of Testing and Calibration Laboratories. An accredited lab has been audited on a regular basis by an independent third party and has proven that it meets the management and technical systems requirements of the standard and the laboratory has adequate equipment to perform the tests or calibrations. In addition, the lab must demonstrate that it has adequate, technically competent personnel to perform the calibration and/or tests.
Q: Why would I want to use an accredited lab?
A: The benefit of using an accredited lab is that you are assured that the lab has been audited to an international standard based on demonstrating their competence in performing the calibrations and/or tests. Prior to laboratory accreditation, the only way to determine supplier quality was to perform your own audit of the lab. Accreditation provides assurance that the lab's processes were independently verified by a third party. For more information, please view our white paper on Accreditation and 17025.
Q: What is an accredited calibration?
A: An accredited calibration is a calibration that is within an ISO/IEC 17025 accredited lab's approved scope of accreditation which demonstrates the lab's technical competence to perform those measurements.
Q: What is the difference between a Transcat accredited vs. a non-accredited calibration?
A: The processes, datasheets, standards, and personnel used during a calibration, whether accredited or non-accredited are the same for any Transcat calibration.
A non-accredited calibration, also referred to as a “commercial calibration” has the following attributes:
- A certificate of calibration will be issued. The certificate will not have an accreditation logo or a statement of traceability
- Basic information that identifies the instrument, calibration/due dates, a statement of conformance either being in or out of tolerance, lab and technician performing the calibration
- Laboratory assets used and the environmental conditions
- May or may not contain the actual data report depending if specified at the time of service
The main differences for an accredited calibration are:
- An accreditation logo will be present on the calibration documents
- The calibration will be traceable to SI units through NIST or other National Metrology Institutes (NMI)
- Most importantly, the data report includes the measurement data and measurement uncertainties
Q: How do I know whether I need an accredited calibration or just need to use an accredited lab?
A: The decision whether an accredited calibration is required is solely a customer’s decision to make a proper determination. This decision is based on several factors. One critical factor is whether your company must meet any regulatory requirements. A number of these requirements specify that accredited calibrations are required.
Another factor is your company’s quality policy. Many policies will specify the need for accredited or traceable calibrations. Some policies may simply state that an accredited lab must be used which may or may not require an accredited calibration.
Finally, you must consider the use of the instrument and the amount of risk you are willing to accept with regards to the measurements obtained with the instrument. If you are using this instrument to calibrate other instruments within your company or process, an accredited or traceable calibration may be required. In the end Inspection, Measurement, and Test Equipment (IMTE) that is used to determine acceptance of product or services is not traceable without an accredited calibration. The purpose of the accreditation process is to identify, quantify, and minimize risk throughout the measurement traceability chain, starting with each country’s National Metrology Institute and ending in the individual acceptance measurements made on products and services. While Transcat encourages our clients to understand this importance, it is ultimately each of our client’s decision to determine what amount of risk is acceptable to their product/service.