
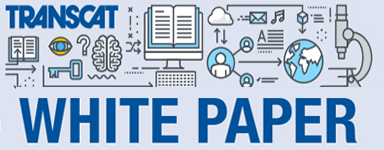
Limited calibration…it’s not a dirty word!
A Good Metrology Practice (GMetP) for a Calibration Service Provider (CSP) is to flag, mark or identify a unit that has NOT been fully calibrated to the Original Equipment Manufacturer’s (OEM) published specifications. This paper will discuss the quality and business impact on real world applications of this practice. It will discuss reasons a metrology lab may offer, and the reasons a customer may request a limited calibration. The factors, benefits, risks, precautions and actions associated with a limited calibration will be covered from the customer perspective. Additionally, the paper will offer ideas on how to manage equipment with a limited calibration and how to respond to questions during an audit. Illustrative real world examples in dimensional and electrical parameters will be used to reach a broader audience.
This is the final paper in a sequence of three related papers. The first paper Business’ Impact on Metrology, presented by Howard Zion, covers the customer’s decision making process and how that sets the expectation for what is to be accomplished in a calibration lab; and the calibration lab’s capabilities and understanding of the customer’s requirements. The second paper covers Metrology’s Impact on the Process (i.e., how the customer will use the technical calibration information in their process), presented by Jeremy Sims.
The information provided in these three papers will benefit conference attendees by providing practical information and exploring the inter-relationships between Business Decisions, Metrology Practice, and Process Impact.
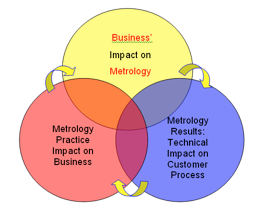
Introduction
The metrology field has some unique practices that have developed over time from a wide variety of standards, regulation and common sense. Within the field, these practices are collectively known as Good Metrology Practice (GMetP). Generally, these practices are designed for the internal operations of a metrology laboratory to increase the confidence in the laboratory’s measurement results and will have little visibility to the equipment user. However, some of these practices have effects that extend beyond the halls of metrology and show up in the Calibration Certificates, Test Reports and the Calibration Labels supplied to the metrology laboratory’s customers and have the potential to impact the customer’s quality and business. One of these practices is the issuance of a Limited Calibration Certificate and label. A limited calibration is a unit that has NOT been fully calibrated to the OEM’s published specifications.
For example, a customer has specified that all calibrations are to be completed against full manufacturer's specifications with a test uncertainty ratio (TUR) of four to one (4:1). However, once the unit arrives at the metrology laboratory, the lab determines that it does not have the test equipment necessary to calibrate one of the functions specified by the manufacturer. Since the customer has specified what the unit is to be calibrated against, full OEM specifications, the lab will contact the customer for approval for an exception for this function. Once the customer grants this approval, the metrology lab will issue a Limited Calibration Certificate and place a Limited Calibration Label on the unit.
Purpose and Reasoning
The purpose of a calibration label is to inform the user as to the status of the equipment. Can the equipment be used, has the calibration expired or will it expire during the next period of use? Likewise, the purpose of the Limited Calibration Label is to alert the user that something is different about this piece of equipment than what is normally expected. The objective of the limited calibration label is to drive the user of the equipment to find out what that difference is and determine what the potential impact could be on using that piece of equipment. There are many possible reasons for a metrology lab to offer a limited calibration and there are some very good reasons a customer may request a limited calibration. The following are some of the most common situations where a limited calibration may be offered or requested.
Out-of-Tolerance, Not Adjustable, Not repairable
The most common reason a metrology laboratory will contact a customer and request approval for a limited calibration is the case when a unit is found in an out-of-tolerance (OOT) condition and the unit is not adjustable and it is not repairable. This frequently happens with dimensional gages. For example, let's take a Class X, Cylindrical Ring Go-Gage with a 1 inch (25.4 mm) diameter which has calibration limits of 0.99994 inches (25.398476 mm) and 1.00000 inch (25.4 mm). The metrology laboratory reports a worst-case measurement of 0.99993 inches (25.398222 mm), which means the gage is out-of-tolerance. It is a solid gage that is not adjustable and cannot be machined or repaired to decrease the diameter of the hole. In this case, the customer has only two choices, either replace the gage or give the metrology lab approval for a limited calibration. The metrology lab offers to provide a limited calibration for the gage against a Class Y tolerance, which has calibration limits of 0.99991 inches (25.397714 mm), and 1.00000 inches (25.4 mm). The practice of down-grading gages to the next lower class is common. Since the gage was manufactured and engraved as a Class X gage anybody picking up the gage would assume it has been calibrated and passed the Class X tolerance. However, in this case, it was not, and the metrology lab put a Limited Calibration Label on the unit. The limited calibration label is a safeguard to prevent an unsuspecting user from using the unit as a Class X gage.
Failure / Out-of-Tolerance, Adjustable, Repairable
The next case can happen when an instrument has an operational failure or is found in an out-of-tolerance condition where there are adjustments for the unit, but the adjustments do not bring the unit back into specification. At this point, the unit will need to be repaired to bring the unit back into the manufacturer’s specification. Now the customer has a few choices, replace the unit, have the unit repaired, or approve a limited calibration. Replacing the unit is the easiest option and offers the least amount of risk, but this option is likely the most expensive. There may also be some issues with replacing the unit. Some industries require a process to be validated and any change in the manufacture and model of the instrumentation in this process will cause the entire process to undergo a re-validation. This can be a serious problem if the specific model is obsolete and no longer available. Repairing the unit offers similar benefits to the replacement option, but again it will have an additional cost. There is also the chance that a repair is just not possible. A unit could be obsolete and no longer supported by the manufacturer, at which point an aftermarket repair house may still be able to repair the unit if the parts are still available. It is also possible that the repair cost far exceeds the replacement cost and the unit is beyond economical repair. This again leaves the option for a limited calibration. A limited calibration may be possible if the operational failure is not on a function required by the customer, or the out-of-tolerance condition is not large enough to affect the customer process.
Lab Standards Not Available
Occasionally, a metrology laboratory might not have all the necessary equipment to fully calibrate an instrument. After all, metrology-grade equipment can be extremely expensive, and equipment manufacturers can place specifications on some unusual parameters, functions or features. So, for practical and economic reasons, a metrology laboratory may lack the capability to calibrate every function. Another possibility is the metrology lab may have the capability to perform the full calibration, but one piece of the laboratory’s equipment may be out for calibration, so they temporarily lack the capability. If the customer cannot wait for the metrology laboratory’s equipment to return, they may be offered a limited calibration for the parameter, function, feature or range which cannot be completed.
TUR / Measurement Uncertainty Requirements Not Met
There are measurement situations where the metrology laboratory’s ability to achieve the customer’s Test Uncertainty Ratio (TUR) requirements cannot be met because the equipment, technology, or method are just not practical for most labs. One such parameter is Relative Humidity calibration. For example, a customer sends a humidity meter that has a specification of ± 1.0% Relative Humidity and wants it calibrated to the full manufacturer’s specification with a TUR of 4:1. To achieve a 4:1 TUR, the metrology laboratory must have a humidity uncertainty of ± 0.25% Relative Humidity. This level of humidity uncertainty is out of reach for most calibration laboratories. Calibration laboratory uncertainties around ± 0.5% are more common. A laboratory with a ± 0.5% Relative Humidity uncertainty can provide a TUR of 2:1. Since the laboratory’s TUR does not meet the customer’s requirement, the lab should contact the customer and discuss the options available. The customer has two basic options, either accept the 2:1 TUR the laboratory can provide, or change the specification the unit is tested against. The customer could choose to have the unit calibrated to a tolerance of ± 2.0% rather than the manufacturer's specification of ± 1.0% which would effectively meet their 4:1 TUR requirement. The metrology lab would mark this as a limited calibration because it was calibrated to something other than the manufacturer's specification. If the customer accepts the 2:1 TUR, the lab would not mark the unit as a limited calibration. However, both options have the potential to affect the customer’s process and both options must be analyzed and quantified by the customer.
Parameter / Range / Function Not Used
Often multifunction equipment is selected for its wide range of application and flexibility, but when used in production lines and dedicated test stands, only some of the features may be used. In a world of ever-tightening budgets, limiting the calibration of multifunction equipment to only those parameters, functions, or ranges used may reduce calibration cost and not impact the quality of measurements. This is when the limitation request might be initiated by the customer. For example, a customer has several dedicated tests stands with multimeters installed. Each of the multimeters has the parameters and ranges shown in the table below.
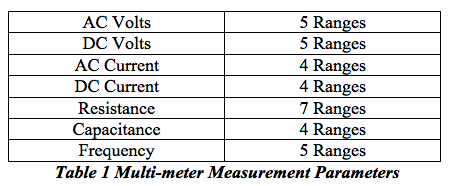
The test stands are dedicated to a single process that only uses two DC Volt ranges and two Resistance ranges. The customer requested that only the ranges he uses are to be calibrated. The units will have a limited calibration, but the amount of time required to calibrate them may be significantly reduced and open the possibility for negotiating a reduced calibration price and ultimately a lower calibration budget for the customer.
Evaluation and Risk Management
A unit with a limited calibration has an increased risk to the customer which requires proper management and should be addressed in the customer’s Quality System. Some elements of a policy on limited calibrations should include an evaluation process, an approval process, the distribution of information to process operators, and a method to flag and monitor the equipment to prevent the unit from being used in another process.
Evaluate
The single most important thing necessary for a customer to know before approving a limited calibration is the potential impact on their process. The equipment in a process was typically chosen based on the manufacturer's specification, and any alteration to these specifications must be evaluated. In the first example, the customer is manufacturing an axle with a diameter of 1.000 inches (25.4 mm). The axle has a maximum diameter of 1.0000 inch (25.4 mm) and a minimum diameter of 0.9995 inches (25.3873 mm). The process uses two Class X Cylindrical Ring gages, one Go and one No-Go, to check the dimensions of the axle. The use of the Class X gages to check the part has a measurement uncertainty of 0.000141 inches (0.003581 mm) and will provide a process uncertainty ratio of 3.54: 1 as shown in figure 1.

When the gages were calibrated they were found to be out-of-tolerance by a count or two. The metrology lab offered to provide a limited calibration for the gages against a Class Y 1.000 inch (25.4 mm) Go gage tolerance, which has calibration limits of 0.99991 inches (25.397714 mm), to 1.000 00 inches (25.4 mm) and the Class Y, 0.9995 inch (25.3873 mm) No-Go gauge tolerance, which has calibration limits of 0.99950 inches (25.3873 mm), to 0.99959 inches (25.389586 mm).. The use of the Class Y tolerance gages to check the part has a measurement uncertainty of 0.000221 inches (0.005334 mm) and will provide a process uncertainty ratio of 2.21: 1 as shown in figure 2.

The effects of the limitation on the process tolerance have been quantified with regards to the measurement uncertainty. If the customer has a minimum process TUR requirement of 3:1, meaning the measurement process must be three times better than the item being measured, then the down-grading the gages to a Class Y tolerance should NOT be approved and the out-of-tolerance units replaced. However, if the customer has a minimum process TUR requirement of 2:1, then the limited calibration would be acceptable. This evaluation should be documented and kept with the calibration records as objective evidence for audit purposes.
Approve
Once the evaluation has been completed it should be reviewed and approved by the appropriate process experts. Each company will have a different structure, but the process owner or expert is likely to be one of the following, the Calibration Coordinator, the Manufacturing Engineer, the Process Engineer, or the Quality Manager. Again, it is highly recommended to document the approval, having a paper trail is never a bad idea when a process is subject to some type of audit.
Inform
After the approval, has been given and the unit has been returned with a limited calibration label, the process operator should be informed about the limited calibration. The process operator is the individual who works with the unit every day and will likely have a question when it has a different label. The process operator is also the individual an auditor will likely question about the equipment used in the process.
Risk Management
The greatest risk associated with a limited calibration is the use of the unit in a different process. To prevent this from happening, the process operators should be trained in the basics of the company’s calibration program, including the limited calibration policy. The company’s calibration management system should track where equipment is assigned along with other basic information on the unit. The calibration records should include the evaluation and approval documents on the limited calibration. With all this in place, one should not fear the questions from an auditor when they spot the limited calibration label. Have no doubt the auditor will find the unit with a limited calibration, just as they have the uncanny ability to find the one unit that has been lost for six months. One should not have any difficulty in defending the decision to approve a limited calibration if the elements discussed here are in place. You should have enough objective evidence that the unit was systematically evaluated with respect to the process, by knowledgeable individuals, approved by appropriate individuals, who informed the process owners, who have received training on the company’s calibration policies.
Summary
A limited calibration is nothing to be feared, it has some value and benefits. However, it is not something that should be blindly approved. To maximize the benefits and minimize the risk all that is necessary is a systematic approach, by knowledgeable people to make an informed decision and proper documentation.
The running theme throughout these scenarios has been the clear communication of expectations between the customer and the metrology laboratory. Effective communication is a two-way street, the customer has a responsibility to know what they need and understand the relationships between their process, test equipment, and calibration results. Once these expectations have been clearly defined and communicated to the metrology lab, it is the metrology laboratory’s responsibility to communicate to the customer any of the expectations that cannot be met. The metrology laboratory does not work in a vacuum, the policies and practices of the lab affect the customer and therefore the lab, as measurement experts have an obligation to help their customers understand and apply metrology information appropriately. Business decisions impact the metrology lab, metrology lab practices impact the results and the metrology lab's results impact business, and business products impact the ultimate consumer, each one of us.
About the Author
Philip Mistretta is a Laboratory Operations Project Manager for Transcat, Inc. He has over 20 years’ experience in the Metrology field including managing an ISO-17025 Accredited Laboratory for over 3 years and currently holds an ASQ-CCT certificate.
Phil was a Lean Manufacturing Engineer for Viatran Corporation in Grand Island, NY for 3 years where he earned his 6-Sigma Green Belt, received his Lean Enterprise training and experience and managed the company’s Calibration Program.
Phil also completed his AAS in Communication Electronics Technology from Central Texas College and his ISCET Associate CET while serving his 9 years of active duty in U.S. Army. He received his Metrology training at Lowery Air Force Base in Denver, Colorado in 1987, and was an Honor Graduate of the U.S. Army Secondary Reference Laboratory course covering DC & Low Frequency, Physical & Dimensional, and RF & Microwave Measurements in 1993 also at Lowry AFB.